Jun 9, 2022
Part 4: Dream Team! Warehouse Management 101: Process & Best Practices
Welcome to the fourth installment of our Dream Team series. Last week, we heard from Brady Thames, VP of Marketing & Sales at TA Services. He shared some insights on the importance of developing a trusted partnership between a shipper and its full-service 3PL provider. Today, we’re hearing from David Bowers, our VP of Warehouse Operations.
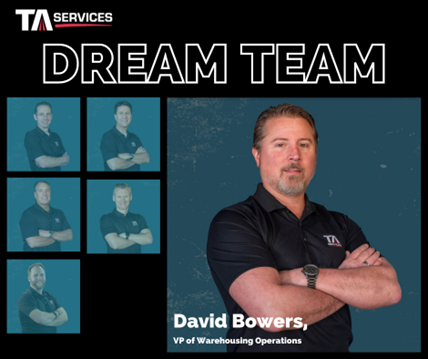
David has worked in operations for more than 25 years, and today he oversees the warehousing and fulfillment operations at TA Services. With all that experience, we asked David to share his best practices and warehouse management tips for making your warehousing and fulfillment operations more efficient.
Why Warehousing and Fulfillment Should Be Top Priorities
Customers’ expectations are growing, which is putting pressure on warehouses to deliver. Consumers are ordering more frequently and expecting faster fulfillment. When your warehouses and fulfillment process are as efficient as possible, you can meet those expectations and improve customer satisfaction. But order fulfillment involves more than just picking and packing, the entire process — from receiving to shipping — needs to run smoothly. By improving your warehouse operations and order fulfillment process from start to finish, you can improve your picking speed and accuracy, reduce your labor costs, and streamline your overall supply chain.
Best Practices for Efficient Warehousing and Fulfillment Operations
No two warehousing and fulfillment strategies should be the same. Every shipper has their own needs and goals. But there are still a handful of best practices that every business should keep in mind when building their strategy. Here are our top four best practices:
1. Leverage the best technology on the market
Warehousing and fulfillment technology has evolved rapidly over the last several years. It’s important to adapt with this technology in order to improve efficiency and accuracy. And ensuring all your technology is integrated will help keep all your data in one place.
A warehouse management system (WMS) is software used to manage the day-to-day operations of your warehouses, including processing the movements of goods and tracking inventory. Choosing the right WMS — that can integrate with any other systems you utilize for your supply chain, such as your transportation management system (TMS) — will help monitor materials and products as they flow through your supply chain.
There are also a number of technology systems that should be implemented to help keep your warehouses safe for your employees. Some of the types of safety technology we use at TA Services include:
- Safety Blue Lights
- Fork Level Lasers
- Aisle Laser Lines
- Fork Level Cameras
- Dock Alert Lights
2. Be strategic with warehouse design and locations
Choosing the locations of your warehouses is an important first step in your warehouse management strategy. When determining where to open your warehouses, think about where your customer base and supplier network are located. Proximity to customers and suppliers should be a top consideration. It’s also important to research real estate costs and tax rates in the regions are you considering opening a warehouse.
Once you have your locations selected, you must prioritize the design of your warehouses. Smart warehouse designs — keeping in mind storage strategies and traffic patterns — will allow you to best optimize the flow of your warehouses. My team recently shared four steps for maximizing warehouse design:
- Step 1: Know what you are storing and be smart about storage mechanism options
- Step 2: Engineering wholistically — know where the product is going and the best way to get it there
- Step 3: Reduce bottlenecks
- Step 4: Choose the right partner
3. Identify inefficiencies and their root causes
You should always be looking for ways to improve your warehouse and fulfillment operations. Issues like inaccurate inventory tracking and inefficient picking can lead to major problems across your entire supply chain. Key performance indicators (KPIs) are an important tool for monitoring your success and shining a light on potential inefficiencies. At TA Services, we get to know our customers’ challenges and goals to determine which KPIs they should be tracking.
To optimize your warehouse operations, tracking KPIs is just a first step — taking the steps to identify the root causes of your challenges or inefficiencies is how you can truly make a difference. TA Services performs a root cause analysis to get to the sources of our customers’ issues and enact change.
4. Don’t be afraid to outsource your warehousing
It’s important for businesses to put their greatest effort and most time into their core competencies. Focus on what you’re good at and what’s most important to you — keeping your customers happy and growing your business. And for those other areas, like warehousing and fulfillment, lean on a partner with the expertise to help you not only manage the day-to-day operations but create a long-term strategy for success.
TA Services not only has that expertise, but we also have more than 2 million square feet of dedicated and multi-client warehouse sites. We’ll work with you to identify the right space for your needs, even if that means growing our future site locations with you and your business goals in mind.
If you’re interested in learning more from David or working with his team, reach out today to see how TA Services can help improve the efficiency of your warehousing and fulfillment operations.
Join us again next week for a new installment of our Dream Team series. We’ll be hearing from Andrew Welling, Director of Cross-Border Services at TA Services, who will be sharing his tips for overcoming today’s cross-border shipping challenges.